
Zensimu’s Lean Game creates just such a simulated workshop. Games can provide a perfectly safe, intuitive way to simulate this continuous learning framework and allow teams to practice implementing the philosophy into their actions. The company as a whole must be well versed in the JIT philosophy and embrace an operational excellence mindset. Because buffers are being removed or decreased (less work-in-process stock, short customer delivery cycles, etc.), any problem that arises can become quite consequential. It is important for all teams who wish to successfully implement JIT understand that the approach is not without risks. How does Zensimu help you train your teams to Just-in-Time? Results will always vary depending on the business and production context, but the JIT model is quite popular and well-received in most manufacturing environments. They observed considerable overall improvements at all their production sites, such as:ģ0% reduction in reworks and scrapped products/parts

One of the first western companies to leverage JIT in manufacturing was Hewlett-Packard. How does Just-In-Time work? What are its advantages?Ĭompanies that incorporate the JIT methodology observe multiple benefits, including but not limited to: reduction in production costs, quality improvement, improvement in internal and supplier relations, reduction in needed storage space, decreased manufacturing time, improved customer service, etc. Fortunately, with modern digitalization tools, data collection can be automated for increasing the efficiency of any administrative tasks. Bureaucratic procedures and steps obviously weigh down manufacturing and production processes. The Six-Sigma approach can help with the goal of getting it “Right the First Time”. Part defects can require extra corrective processing or even result in scrapping the part altogether, which is a loss of all material and invested efforts, or even worse-client returns and damage to a company’s reputation. Breakdowns cause delays and result in additional costs, which can be minimized by implementing preventive maintenance on equipment with regular checks to avoid unexpected issues. All machines should ideally operate continuously with controlled performance. Waiting for any product, part or information from any source must be kept at a minimum. To increase flexibility, each step in the process should take the least amount of time possible. Otherwise, the resulting “waiting”, or even excess, inventory becomes an immobilized asset, which absorbs company capital with no added value.
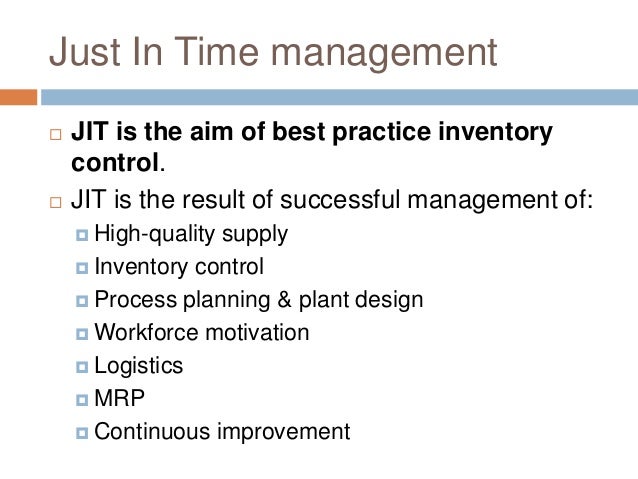
At every step of the production process, products must arrive at just the right moment of utilization. The main principles of JIT are called the Five Zeros:
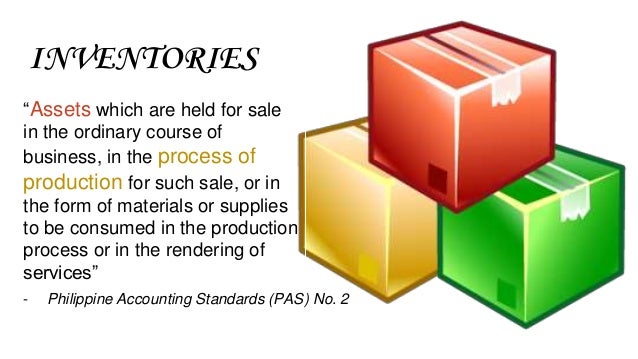
It is also applied to increase flexibility within the entire production line and supply chain to better and more quickly respond to customer demand within a limited cycle period-from assembly to delivery. An essential component of Lean Manufacturing, Just-In-Time (JIT) is a methodology for establishing and maintaining the smooth, continuous flow of products in the production process with minimal buffers between steps.
